Visitamos el taller de Villaverde donde Citroën ensambla las baterías para el C4 eléctrico
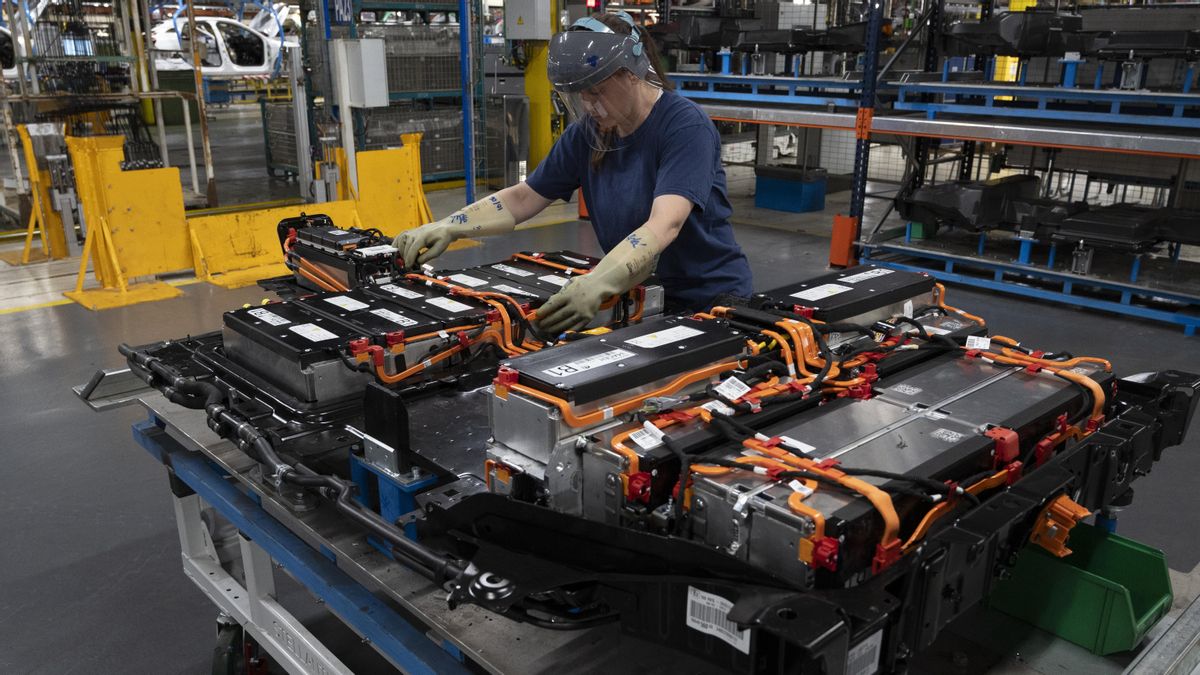
Los dedos de una mano no bastan para contar las veces que hemos podido visitar la fábrica que el grupo Stellantis tiene en el barrio madrileño de Villaverde. La que ha organizado Citroën hace pocos días ha revestido, sin embargo, la singularidad de poder acceder por primera vez a su nuevo taller de baterías, donde se ensamblan los módulos que utilizan para funcionar el C4 y el C4X eléctricos, que se producen aquí en exclusiva para todo el mundo.
Durante el año pasado, salieron de la histórica planta -que comenzó a operar en 1952 por iniciativa de Eduardo Barreiros- un total de 92.589 unidades del Citroën C4. De ellas, 81.470 (un 88%) correspondieron a versiones equipadas con motor de combustión y las 11.119 restantes (12%), a variantes eléctricas, tanto del C4 convencional como de su carrocería sedán (C4X).
Los responsables de producción de Villaverde, encabezados desde fechas recientes por Diego Rivas, nos informan de que cuentan con la capacidad para despachar hasta un 50% de modelos eléctricos, pero para eso tiene que acompañar una demanda que de momento no es todo lo sólida que se necesitaría.
Lo que sí tira -y mucho- del mercado en la actualidad es el volumen de pedidos de las nuevas versiones de hibridación ligera, o mild hybrid, que han llegado al C4 como a otros modelos de Stellantis en los últimos tiempos. Rivas y su equipo estiman que en este 2025 van a concentrar la mitad o más de la producción de la planta.
Es digno de mención que, en una fábrica tan compacta como esta -sobre todo si se la compara con la inmensidad de la de Figueruelas (Zaragoza), por ejemplo-, Citroën/Stellantis es capaz de producir en una sola cadena de montaje las tres variantes de motor del C4. Una adecuada logística es el secreto que permite que cada vehículo que circula por la línea disponga en tiempo real de los componentes y la utilería necesarios para su correcto ensamblaje.
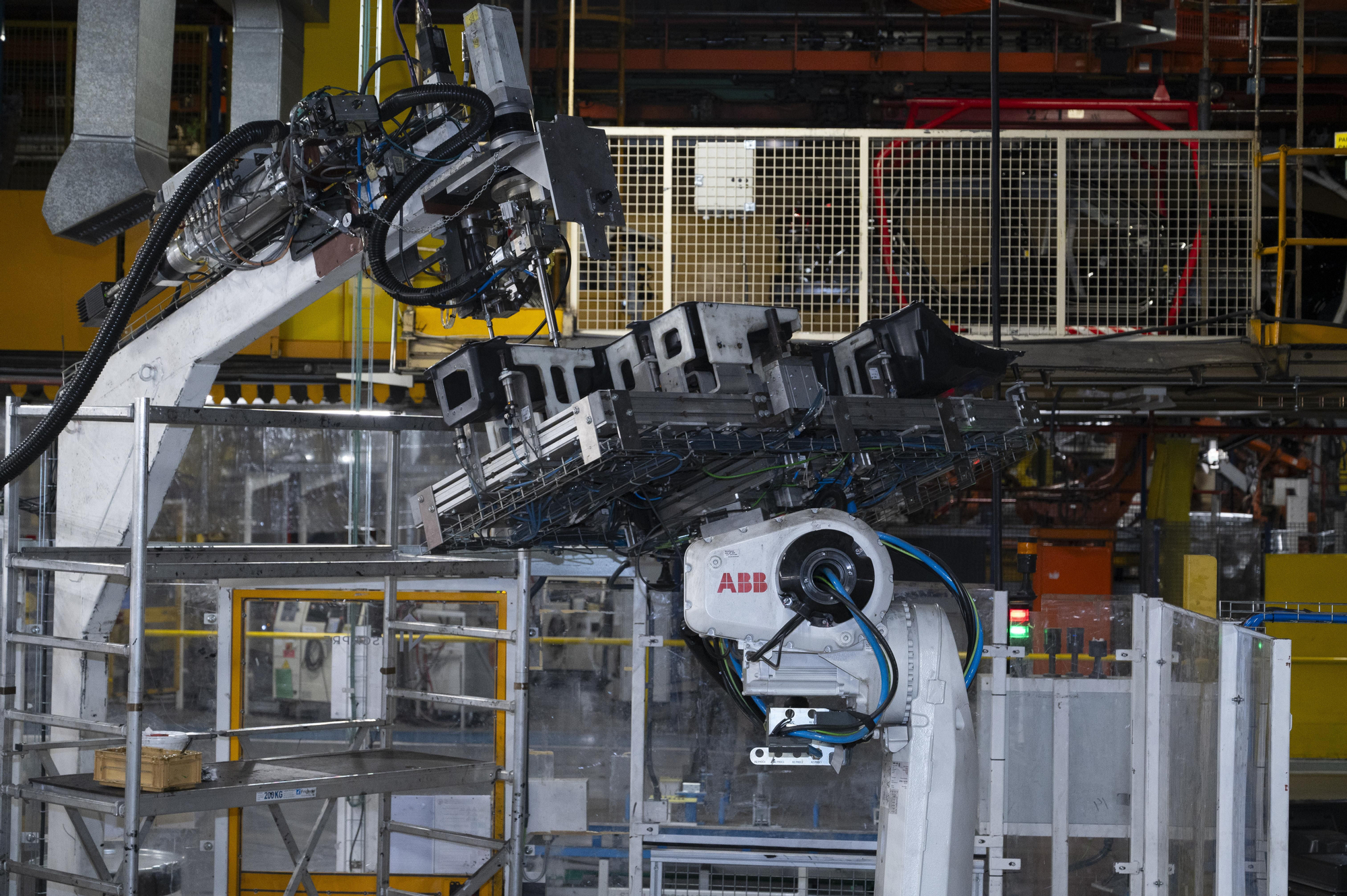
En el corazón de la factoría se ha hecho ahora espacio para montar el taller donde se ensamblan los módulos de batería procedentes del gigante chino CATL, con el que Stellantis ha acordado construir una gigafactoría precisamente en Figueruelas. La posición central de esta pequeña instalación obedece a que, una vez terminadas y colocadas sus cubiertas, las baterías se incorporan al proceso sin fin de la única línea de montaje de la planta, donde -como hemos visto- se coloca indistintamente un motor de gasolina o uno eléctrico, así como cualquier extra solicitado por un cliente equis.
La batería del ë-C4 consta de 18 módulos, cada uno de los cuales pesa 12 kilos, en la versión de 50 kWh y de 17 módulos en la más reciente de 54 kWh. La primera opera con un voltaje de 394 V y ofrece una autonomía de alrededor de 360 kilómetros; la segunda, a 375 CV, extiende el alcance a cerca de 420 km. Ambas vienen a pesar unos 340 kilos con todas sus piezas montadas.
Para los amantes de los datos, añadiremos que ambos dispositivos presentan unos 160 puntos de atornillado, 25 conectores o bus bars y 18 y 17 -respectivamente- bases de refrigeración. Los trabajadores tienen a su disposición 18 herramientas de atornillado diferentes.
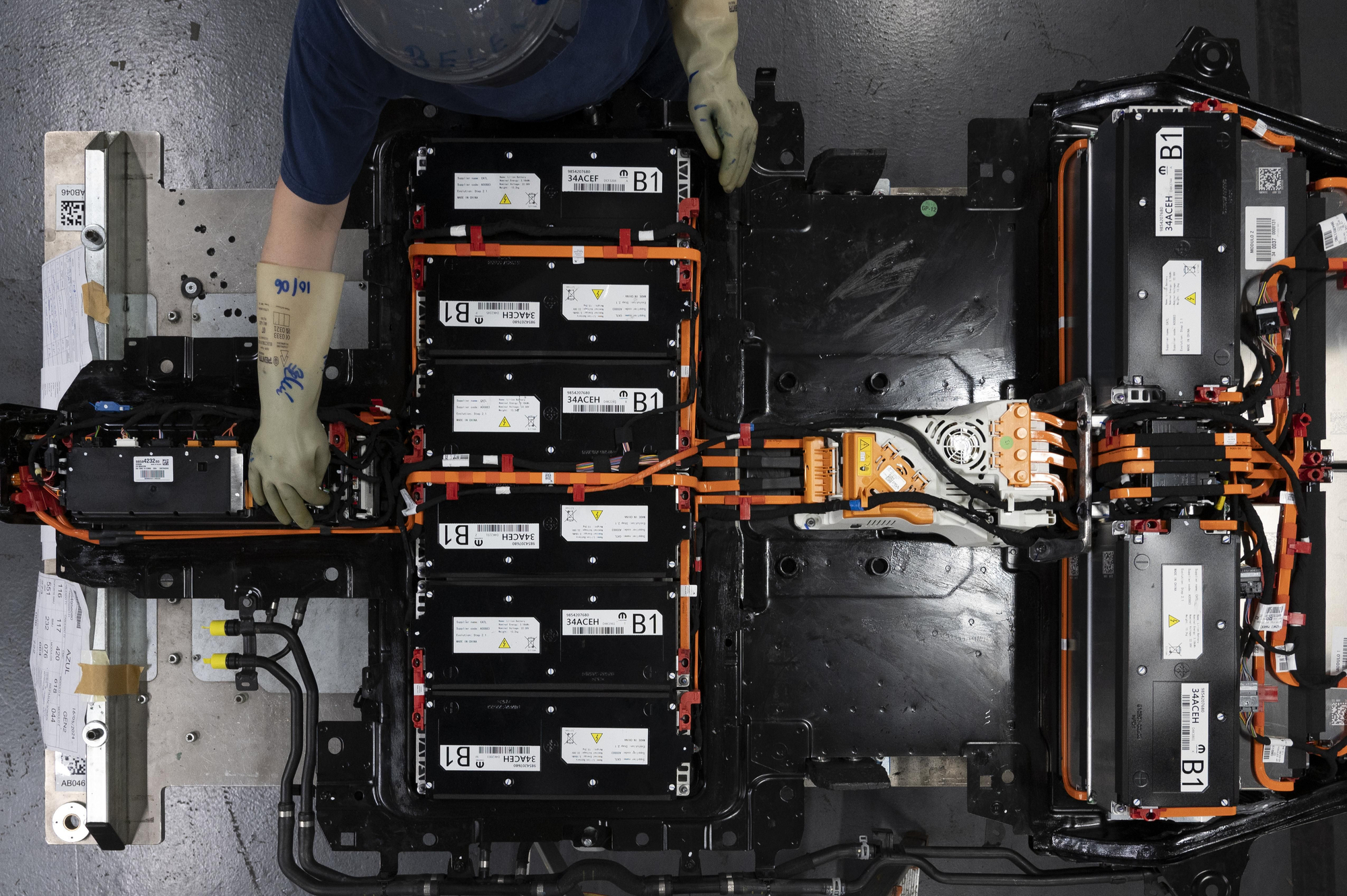
Tecnología específica
El taller ocupa una superficie de 2.000 metros cuadrados y se compone de 16 estaciones de trabajo, con la capacidad de producir 11 baterías por hora, a razón de 5,45 horas por cada dispositivo. Dispone de elevador de aprietes bajo batería, robot de sellado, almacén de polimerización y línea de ensamblado automatizado. Su capacidad de producción a cadencia plena es de 50.000 unidades anuales.
Antes de su ensamblaje en la plataforma e-CMP, base técnica de los Citroën ë-C4 y ë-C4 X, las baterías se someten a controles de calidad que aseguran su correcto funcionamiento. La instalación está equipada con las últimas tecnologías en materia de testeo eléctrico y estanqueidad, y en ella se realizan pruebas de funcionalidad, aislamiento y fugas.
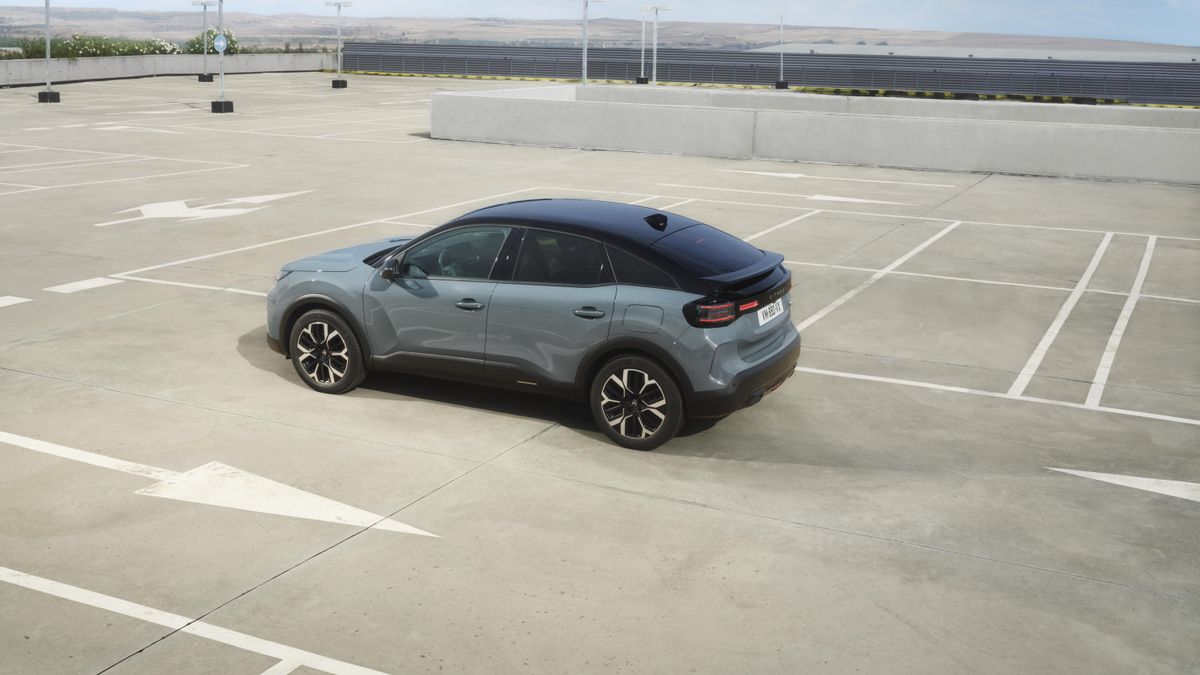
En el caso concreto de Villaverde, el proceso de montaje de los vehículos se halla en mitad de una operativa que comienza con la soldadura de las piezas que conforman la carrocería, pues aquí no existe estampación previa. A continuación, el coche entra en Pintura, donde, aparte del color y el barniz, se aplican tratamientos anticorrosivos y de impermeabilización y lacado.
Justo después llega el trabajo de montaje propiamente dicho, que lleva cerca de ocho horas y comprende el ensamblaje de todos los componentes y accesorios del vehículo, además del matrimonio final -un momento siempre mágico en la producción de automóviles- entre la carrocería y el chasis con su motor correspondiente.
De los últimos pasos del proceso de producción se encargan los controles de calidad, complementarios a los que se realizan en cada una de las áreas, y todo ello se acompaña del despliegue de coordinación logística antes referido, sin el cual cualquier tarea dentro de la planta sería sencillamente imposible en los tiempos actuales.